What to Expect During a Commercial HVAC Installation Project
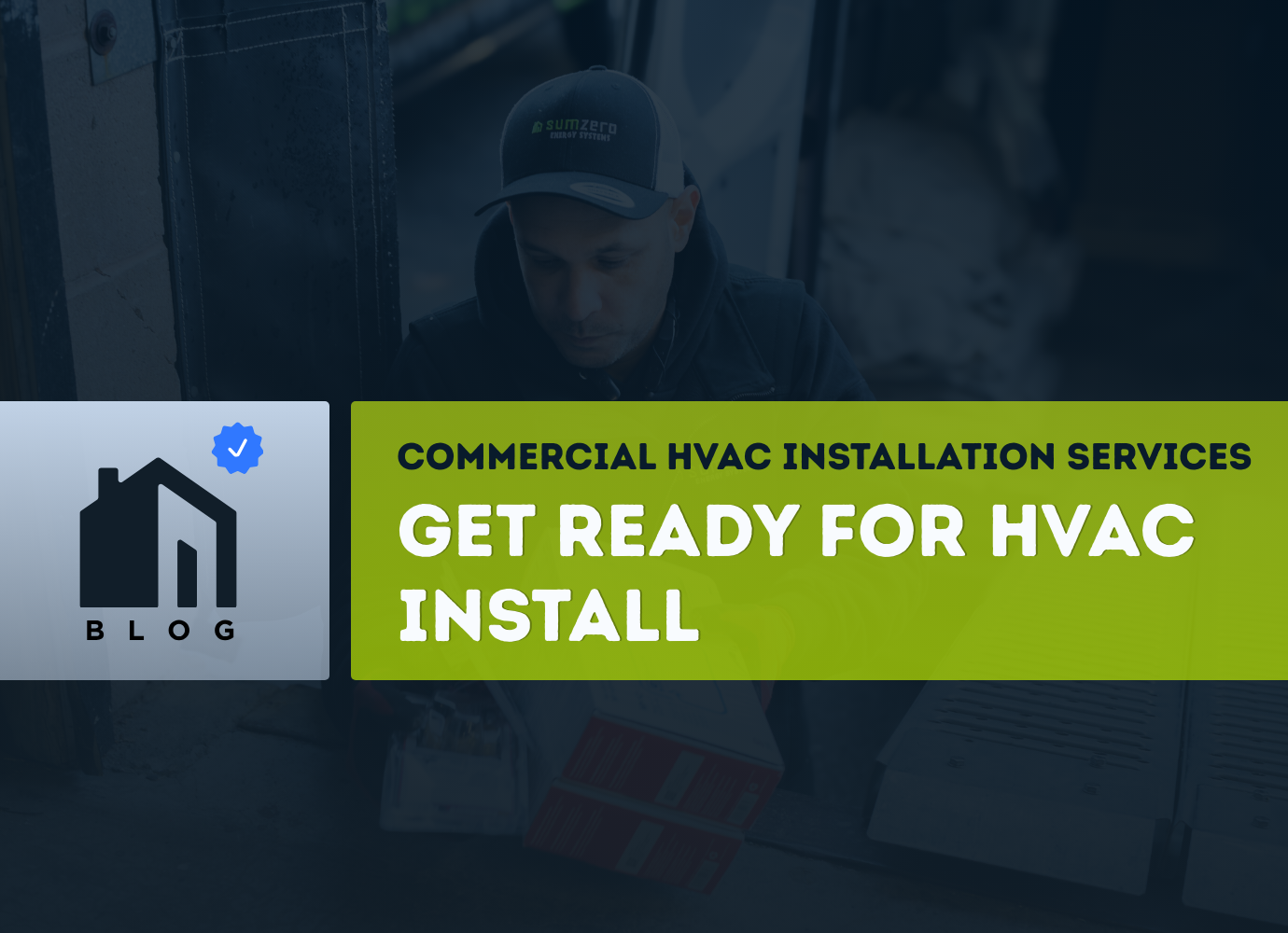
Understanding the Commercial HVAC Installation Process
Starting a commercial HVAC installation project in Massachusetts can feel overwhelming. With so many factors to consider — from system type to zoning permits — it’s crucial to understand the major phases you’ll go through. A well-planned HVAC upgrade not only improves indoor comfort but can significantly cut down energy costs and maintenance headaches over time.
One of the most important things to clarify upfront is that this is a multi-stage process. Each step plays a vital role in ensuring your system is designed to meet the unique demands of your building and the unpredictable New England climate.
Initial Planning and Site Assessment
Every successful HVAC install begins long before any machinery arrives. A thoughtful planning process ensures the equipment you choose is properly sized, cost-efficient, and positioned for long-term reliability.
- Evaluate building size, insulation level, and usage patterns
- Review zoning codes and permit requirements for Massachusetts
- Choose between system types like ducted, ductless, and efficient rooftop units
- Determine energy goals — such as heating optimization or smarter zoning
One often-overlooked insight: underrating equipment size can cost more in the long run than overspending upfront. An improperly sized system will wear out faster and struggle to maintain stable temperatures.
It’s during this planning stage that you’ll lock in important decisions about airflow, cooling needs, budget, and sustainability. Whether you're retrofitting or starting fresh, this phase sets the tone for efficiency and durability.
Equipment Delivery and Preparation
Once designs are finalized and permits obtained, the next step is preparing for delivery of the HVAC units and materials. For many Massachusetts buildings, rooftop HVAC systems offer the best balance of space-saving and air circulation.
The preparation phase typically covers:
- Delivery coordination based on building access and weather conditions
- Site clearance and rooftop access inspections
- Electrical and structural requirements validation
- Pre-staging components to avoid delays
According to Mass Save®, upgrading to high-efficiency HVAC systems for businesses can lower energy usage by up to 30% when combined with professional planning and weatherproofing.
This is a good time to review your disruption plan — find out what areas of your building will be impacted and for how long. Be proactive with tenant or employee communication to maintain safe working conditions during the transition.
[[cta-heatpump]]
Installing Your Commercial HVAC System
With preparation complete, the real work begins. The installation phase typically takes several days to a few weeks depending on the building size and scope. While the timeline can fluctuate due to weather or unexpected findings, following a methodical process keeps the project on track.
Placement of Major System Components
At this point, large mechanical equipment gets positioned, secured, and connected. Rooftop units are installed using mobile cranes, while ducted systems may require access through ceiling tiles, attics, or utility spaces.
Key activities include:
- Mounting air handlers and compressing units on supports
- Sealing roof penetrations to prevent future water leaks
- Integrating with the existing or new ventilation system
- Connecting line sets and drain lines
You might notice teams working around the clock to minimize disruptions in busier locations — especially during off-peak hours for retail or healthcare centers.
Electrical and Control Connections
Modern ducted commercial HVAC systems rely on smart thermostats, zoning controls, and environmental sensors for maximum comfort and cost savings. During installation, your chosen systems will be wired to support automated scheduling, remote access, and energy monitoring.
Electrical work typically includes:
- Routing power supplies to major HVAC components
- Verifying voltage compatibility and circuit integrity
- Setting up programmable thermostats or building management integration
A growing trend in Massachusetts is pairing HVAC upgrades with energy-recovery ventilators (ERVs) to boost indoor air quality and reduce heating demands during cold months.
Once powered, your system is fine-tuned for pressure levels, air distribution, and airflow balance. The final electrical tests ensure that the system runs safely before entering the commissioning phase.
Final Inspection and Ongoing Optimization
Once the physical work is done, the final stretch focuses on testing, fine-tuning, and compliance. This last phase is what elevates a basic install to a long-lasting comfort solution tailored to your specific needs.
Commissioning and System Testing
During commissioning, HVAC teams evaluate performance using diagnostic tools and real-time system feedback. Adjustments are made to airflow settings, refrigerant levels, and motor timing.
Checklist activities include:
- Checking airflow at every vent and return
- Calibrating sensors and thermostats
- Verifying programmable settings and zoning schedules
- Ensuring temperature consistency across zones
It’s normal to find a few things that need adjusting after the first full system run — that's part of a good commissioning process.
Final Inspection and Permit Approval
Before a system is fully considered complete, most Massachusetts towns require a signed-off inspection. Inspectors confirm that:
- The HVAC system complies with local energy codes
- Rooftop units are secure and waterproofed
- Combustible clearance zones are respected
- Ventilation and indoor air quality meet building code
Once inspection is passed, a final approval notice is issued and any project documentation — including manuals and warranty certificates — is handed over.
Smart planning during a commercial HVAC install can add 10-15 years of reliable use, while skipping inspections can lead to problems that void warranties or violate building codes.
Planning for Long-Term Efficiency
It’s easy to celebrate once the HVAC system is in place, but longevity and efficiency require ongoing attention. Regular maintenance checks, filter changes, and seasonal tune-ups keep things running smoothly. Massachusetts homeowners can also look into annual rebates and optimization programs offered by Mass Save® to maximize system benefits and energy savings.
Final tip: request a full training walkthrough for whoever manages your facility or controls the thermostats. Understanding how to monitor your HVAC systems for businesses empowers better decisions — and fewer emergency calls when temperatures drop below zero.
By staying informed and involved from the first conversation to post-install maintenance, Massachusetts building owners can ensure their investment brings real value for years to come.
Maximize comfort and energy efficiency with expert commercial HVAC installation tailored for Massachusetts businesses—visit our service page to start saving with a smarter system today.
Get Commercial HVAC InstalledYou Might Also Like…
Continue learning with handpicked articles that inform and inspire.
Not Sure Where to Start? We’ll Guide You
Let our experts design the right heating and cooling solution—customized for your comfort, your layout, and your energy goals. No pressure. Just clarity.
Request FREE ESTIMATE